By Anastasia Montgomery
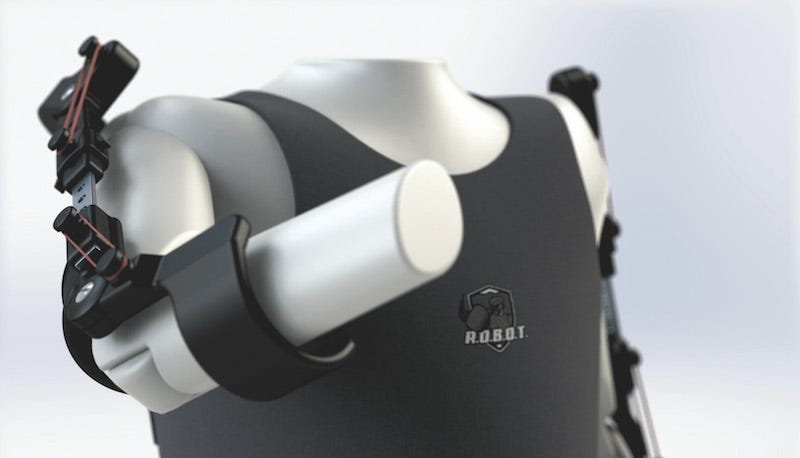
Nearly 20 percent of United States citizens have a disability, according to the United States Census Bureau. With such a large amount of people with conditions that may hinder their ability to participate in daily tasks, there is a great demand for technology to help make their lives easier. The technical term for this technology is called assistive technology, meaning a piece of equipment that improves or maintains the functional capacity of a person with disabilities. However, as 3D printing becomes more mainstream and cost efficient, the assistive technology market has opened up for everyone.
Through UW-Madison senior capstone design projects, students are connected to clients who present them with varying engineering challenges. A UW-Madison mechanical engineering design team of Aevyrie Roessler, Stephen Wisniewski, Joseph Bradel, Shengyu Liu, and William Mann under faculty advisor Heidi-Lynn Ploeg, is working on a piece of assistive technology for a client with Arthrogryposis Multiplex Congenita (AMC). This term describes the rare condition in which a joint is formed permanently in a bent or straight position, affecting movement of the joint. The symptoms of AMC are present at birth and vary in severity but in most cases, it becomes very difficult to move as muscles are underdeveloped and joints are swollen shut. Such is the case for the team’s client, a seven-year-old boy whose upper limbs are affected by the disease. As the client is in school, his father sought help from UW-Madison to make daily tasks easier for his son, like lifting and moving his arms.
Similar to others with AMC, the team’s client had already done some therapy to help his mobility, which consisted of using a metallic exoskeleton that would open the arms to stretch the limbs and loosen the joints. “Our client has gained flexibility, but he still lacks strength in his arms, so our solution was to use bands to suspend his arms in the air so that he could pull his arms down to do daily tasks,” explains communication leader and team member, Stephen Wisniewski. “Even though he has very little bicep muscle, in suspending the arms and working on the triceps and back muscles, his biceps could eventually function normally.”
“We talked to the client about the exoskeleton that he used when he was four,” says team member, Joseph Bradel, “and we talked on how we could improve the design and make it smaller and more comfortable to wear but still functional.” The solution the team came up with is a new exoskeleton design that uses bands and 3D-printed pins to make an affordable and lightweight exoskeleton that will allow the client to move his arms downwards to help his mobility. The prototype that the team had originally made was a vest-like creation that had no bulk, but it lacked the support to render it totally functional. “He’s going to go to school with it, and we want him to be able to put on a sweater and not make it look like he’s wearing some robotic scaffolding.”
Another unique aspect of their design is that it will “grow” with the client, that is, with the help of 3D printed components. “In order to make our design ‘grow’ with the client, we want to make it as easy as possible for his dad to remake parts if they break or need to be scaled up,” says team leader Aevyrie Roessler. “So we will give the CAD designs to the father so he’ll be able to just go to a place with a 3D printer to print out new parts.” According to the father of the client, very little equipment is on the market for people with AMC, since the disease is both rare and affects people differently on a case-to-case basis. His father had found the most reliable source for equipment was through the community he found at AMC conventions, where other people would spread the word about available devices and where to find them. “The advantage of our design is that you cut out going to the doctor and having them give you whatever expensive equipment they have for this condition, or paying another design team to create a whole new exoskeleton each time he grows out of it,” says Roessler. “[Our client’s] dad can just print out the parts for many years to come.” Currently, the upfront cost of materials for the team’s design is just $100. According to the team, it’s not exactly certain how much it would cost to scale up the design for years to come, though with the growth in the 3D modeling business, the cost of printing parts will decrease as time goes on.
Unfortunately, there is no cure for AMC, and without proper development of muscles and tendons, people living with this condition would not be able to move easily without an assistive device like the exoskeleton this team is working on. “Essentially, by strengthening the pushing-down motion, we could strengthen the pulling up motion too, and give the client more functionality in his arms,” says Roessler. “Our hope is that this device can be used as a therapeutic device too, so as he uses it he can get a bit stronger and gain dexterity.”
With the help of 3D printing and clever design, this client can benefit from the team’s product for years to come. Innovations like these will continue to make life a bit easier and not so much of a financial burden for people in need of assistive therapy devices.